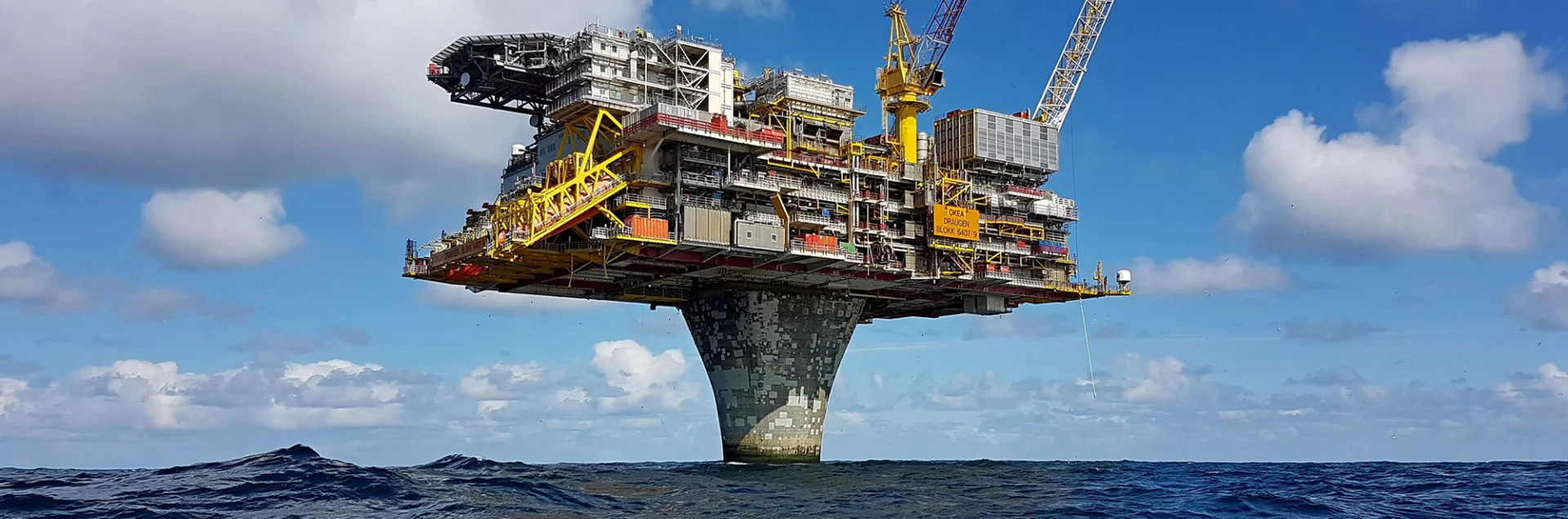
– Improvements at Draugen
The collaboration between OKEA and Safetec on establishing performance requirements for instrumented barriers and following these up started in 2020. After several years of good cooperation, they have now received positive reviews for the improvement work following an audit in this area from the Norwegian Petroleum Safety Authority.
In 2020, OKEA contacted Safetec for advice on how to set up a system for following up the performance of the safety instrumented functions, which are an important part of the barriers against major accidents. From the beginning, Professor Tor Onshus (NTNU) has been a very important part of Safetec's project team in the work to solve these challenges.
Safetec has developed a comprehensive program through close cooperation with OKEA. The work has been based on Draugen being an older facility that was not originally built with requirements to “safety integrity level” (SIL).
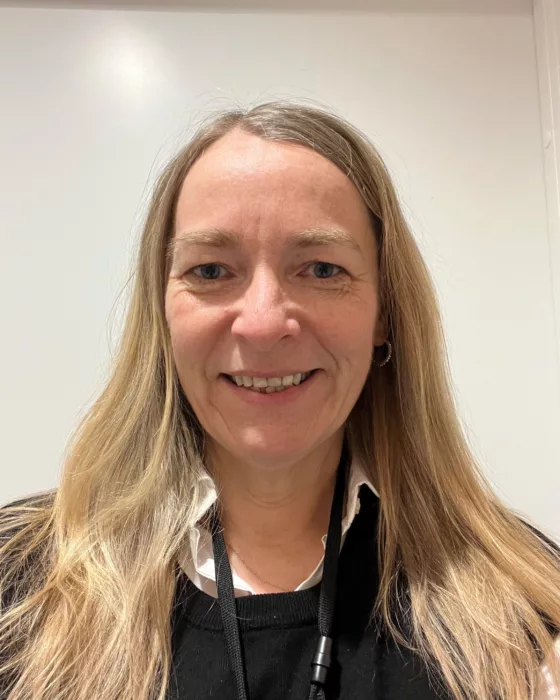
In the collaboration it has been valuable that Safetec has good knowledge and understanding of the challenge of operating an older facility and how this is adapted to today's standards and regulations.
Audit on major accident risk and barriers (spring 2023)
Earlier this year, the Norwegian Petroleum Safety Authority carried out an audit on major accident risk and barriers on Draugen, where they looked at the SIL follow-up scheme, among other things. In the report following this audit, OKEA received positive reviews for its improvement work in recent years.
Among other things, the Norwegian Petroleum Safety Authority states (in the Norwegian report following the audit): "Our impression is that in recent years there has been a positive development in OKEA, where various improvement initiatives have yielded results in the right direction within both technical and operational integrity."
One of the specific points highlighted is OKEA's ownership to and follow-up of results from analyses and verifications, where they specifically mention Safetec's work on establishing a SIL regime at Draugen: "During the audit, we saw several examples of OKEA using external expertise when needed, for example in connection with major internal verifications, analyses related to major accident risk and in connection with the establishment of a SIL regime at Draugen."'
*NB: Both quotes from the report are translated from Norwegian by Safetec.
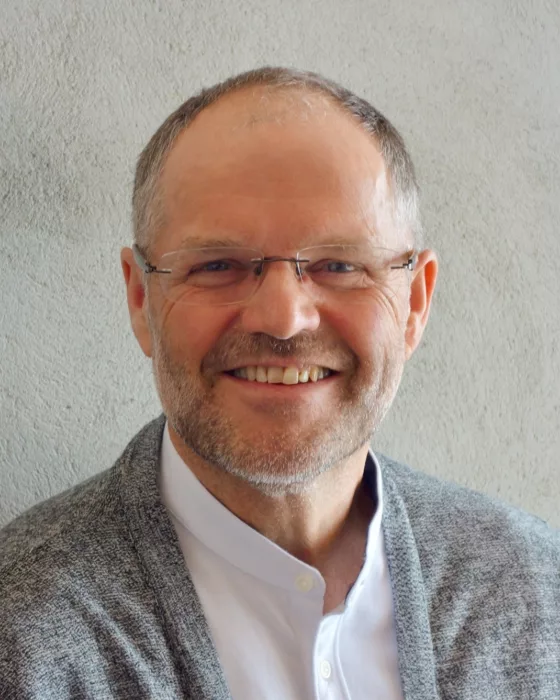
The excellent and close cooperation with OKEA has been particularly positive, and it has also been decisive for the results we have achieved.
Safetec's contribution
One of the most important types of barriers against major accidents on an oil and gas facility is the safety instrumented functions – typically process safety functions in the PSD system and functions in the fire and gas systems (F&G) and in the emergency shut down systems (ESD). For such functions, it is currently necessary to establish and follow up SIL requirements. Functional safety is the slightly more formal term for this field of expertise.
Draugen was not originally built with SIL requirements, since there was no requirement for that at the time Draugen was built. Over the years, modifications have been carried out where SIL requirements have been defined in accordance with existing regulations, but the vast majority of the instrumented functions are from the original construction of Draugen and therefore without defined SIL requirements.
Safetec's work has largely consisted of defining the functions, establishing the performance requirements (SIL requirements), and establishing the "SIL documentation". A systematic approach to this has been established, and procedures have been drawn up for the work on functional safety at Draugen.
Interdisciplinary expertise was required in everything from statistics to being able to understand how the equipment worked and what components/equipment that must function upon a demand. This includes, for example, the operation of transmitters and detectors and logic in the safety systems. Solenoids, valve control panels and valves are of course included, but also fire dampers, relays, circuit breakers and switchboards are described, documentation searched for, and component reliability data established.
– As a side effect through the work, we have also gained a better overview of the existing documentation, and new documentation has been prepared for the SIL follow-up. We are very pleased with that, says Anne Lene Rømuld in OKEA.
SOFUS: A Safetec tool
As an important part of the deliveries from the project, Safetec has also configured its tool for follow-up in operation; SOFUS («SIL in Operations Follow-Up System») for Draugen.
Safetec has developed SOFUS with the aim of following up the performance of the safety systems in the operational phase, and SOFUS is currently in active use on four facilities for three different operators. In addition, Safetec is in the process of implementing SOFUS on a fifth facility. With SOFUS in use on all these facilities, the tool appears to be a de facto standard within this area in Norway.